Golden EDI integrated Blue & Green's 3PL and WMS to their cloud-based ERP and improved their efficiency
Blue & Green is a chemical technology company that specializes in developing and producing cleaning products like carcare products, graffiti removers, and truck-wash solutions, and has been leading product innovation for many years.
With production facilities in Landskrona and sister companies in Norway and Denmark, Blue & Green faced a crucial moment when they decided to move to a cloud-based ERP system and streamline their logistics processes.
The Challenge
Moving to the cloud and integrating systems
Blue & Green had outgrown their previous warehouse space, which led them to outsource logistics and warehousing to a third-party logistics (3PL) provider, Edström, using Nyce as the warehouse management system (WMS).
As David Löwenstein, Product Developer and IT specialist, explains, “We were at a point where it didn’t make sense for us to manage logistics in-house anymore. Our team in Landskrona used to handle the entire process manually, taking hours each day to coordinate deliveries, which wasn’t sustainable as we grew.”
However, integrating BC with Nyce required a reliable solution, which is where Golden EDI came in.
“We were recommended Golden EDI by our partner Bisqo, and they suggested that Golden EDI could handle the integration between BC and Nyce.” – David Löwenstein.
Golden EDI’s integration was crucial for eliminating manual processes, such as Excel-based inventory management, and automating the flow of information between systems.
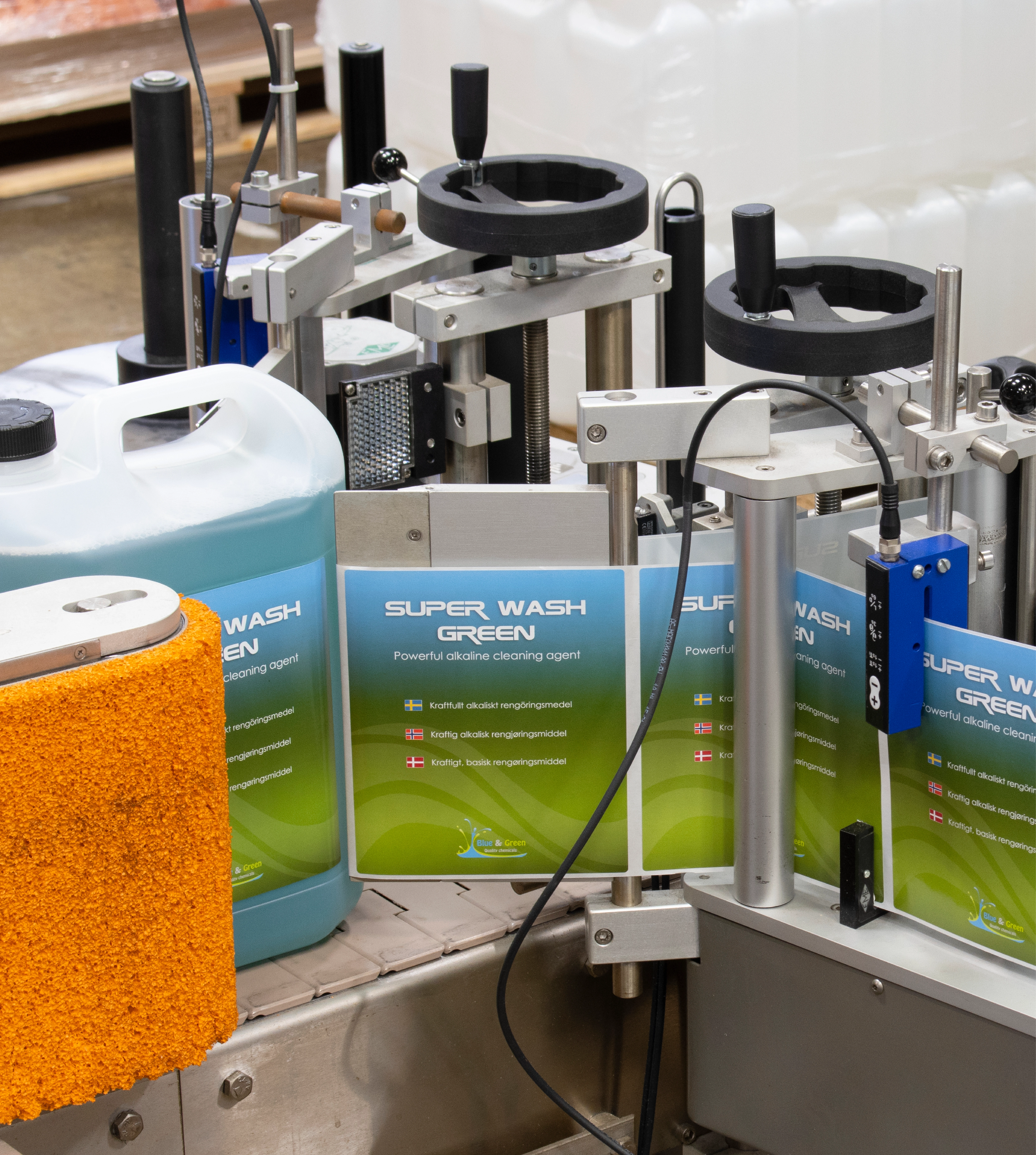
The implementation phase
While the solution added great value, the journey wasn’t without its challenges.
“We had some challenges throughout the implementation phase. There were error messages that were sometimes hard to interpret, and we had to build and test in different environments. But I think this is common with such complex integrations.” – David Löwenstein.
Golden EDI’s team worked closely with Blue & Green throughout the process.
“They were very supportive, and their deep knowledge of BC was invaluable. Whenever we needed help, they were there to support us.” – David Löwenstein.

The result
Improved efficiency and reliability
The results of the integration have made a big difference for Blue & Green.
“We can now register sales orders in BC and release them seamlessly to Nyce, with everything communicated electronically,” David explains.
Another great benefit has been the reduction in manual errors.
“Before, we would sometimes think we had stock, only to find out later that we didn’t. Now, that’s much less likely to happen.” – David Löwenstein.
Last but not least, the integration has freed up valuable time for the team. “We used to spend hours managing logistics in-house. Now, with the 3PL handling deliveries and Golden EDI ensuring everything is synced, we don’t have to worry about that. If we hadn’t integrated these systems, we’d still be doing a lot of manual work.” – David Löwenstein.

Ongoing collaboration
Blue & Green has been happy with the level of support from Golden EDI. “We’ve been very happy with the relationship, the team’s support has been outstanding, and whenever we’ve needed help, they’ve been there for us.” – David Löwenstein.
The partnership is far from over, as Blue & Green is currently evaluating more automation possibilities.
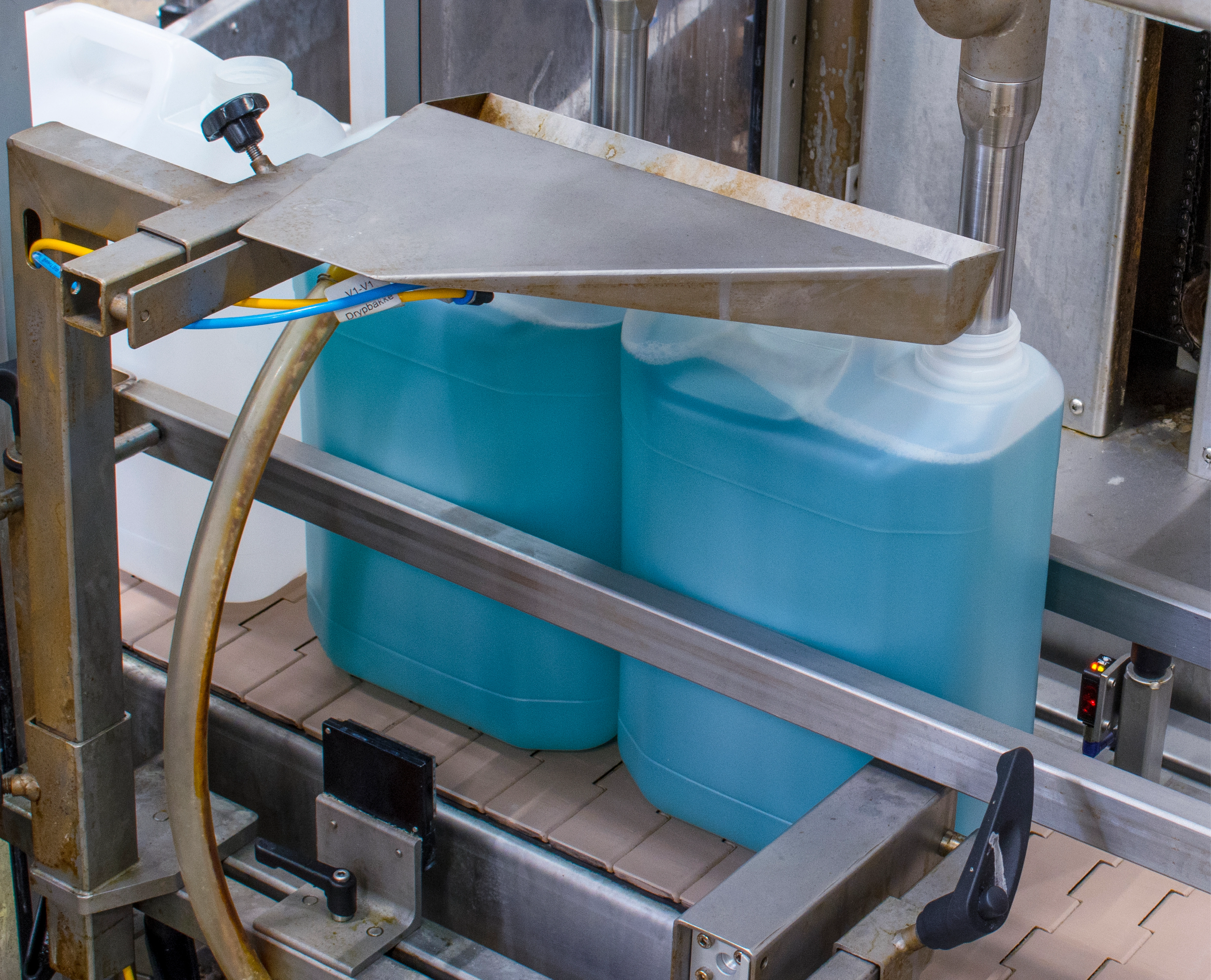
Conclusion
Reflecting on the collaboration, David has no hesitation in recommending Golden EDI. “Absolutely, I’d recommend Golden EDI. In fact, I already have”.
For Blue & Green, the partnership with Golden EDI has been a game-changer. What was once a time-consuming, error-prone manual process has been transformed into a streamlined and reliable one. As Blue & Green continues to grow, the future looks bright, and Golden EDI looks forward to delivering even greater efficiency and value.
